刘祥贵1,2,3,余嘉裕3,陈润宇1,梁雁扬2,3,潘春阳1*,
(1.广东工业大学,广东 广州 510006;2.佛山市南海区瑞联胶粘制品有限公司,广东 佛山 528200;3.广东华通新材料科技有限公司,广东 东莞 523591)
本课题选用低分子量聚丙二醇(PPG1000)与二异氰酸酯(TDI、MDI、IPDI)为原料,制备无溶剂型聚氨酯胶黏剂应用于纵向拉伸聚丙烯(MOPP)的复合中,研究了反应时间、反应温度、异氰酸酯(NCO)与羟基(OH)的摩尔比即R值以及异氰酸酯种类对聚氨酯胶黏剂合成和性能的影响。研究发现,聚氨酯在反应时间为150min,反应温度为70℃的条件下合成最佳;R值(异氰酸酯基与羟基的物质的量之比)越大则初始黏度和平均剥离力越小;异氰酸酯中TDI的使用性能最佳。
聚氨酯;无溶剂;胶黏剂;复合包装;绿色环保
2.1 反应时间对固化剂合成的影响
反应时间对聚氨酯固化剂合成有着重要的影响,如果反应时间过短,聚氨酯固化剂不能达到理论的NCO含量,如果反应时间过长可能更容易导致原料的与空气接触变质或导致产物发生副反应,使得聚氨酯固化剂性能下降、增加反应成本等问题。
从图1可以看出,聚氨酯固化剂在反应时间为150min达到了理论的NCO含量的值13.05%,当反应时间低于150min时,NCO含量远远大于理论的NCO含量值,原因是反应时间过短,体系内残留了较多未反应的异氰酸酯基团,并未与多元醇完全反应。当反应时间超过150min后,继续延长反应时间可能会导致过量的异氰酸酯与水发生反应,或是引发异氰酸酯自身出现二聚、三聚等副反应,使得NCO的含量低于理论值。因此,将聚氨酯固化剂合成的反应时间定为150min。
2.2 反应温度对固化剂性能的影响
本实验选用反应温度范围为60~100℃,制备出来的聚氨酯固化剂的外观均为无色透明,无凝胶、无沉淀。图2与图3为不同反应温度合成的固化剂的黏度以及主剂与固化剂以一定比例配制应用于MOPP复合MOPP的平均剥离力。
从图2和3可以看出,黏度随着反应温度的升高而不断增大,而NCO含量随着反应温度的升高不断减小。在60~80℃的反应温度范围内,黏度增长速度不明显,原因是反应温度较低,聚醚多元醇与异氰酸酯反应不完全,体系内游离的异氰酸酯基团增多,固化剂黏度下降,加快反应温度有助于提高反应速率。而在80~100℃的反应温度范围内,黏度增大速度较快,其原因是反应温度升高,聚醚多元醇与异氰酸酯的反应活性增大,反应速率进一步加快,使得黏度进一步增大。除此之外,从图3.3可以看出,反应温度为90℃与100℃时,其测得的NCO含量远小于理论值,可能的原因是当反应温度过高时,产物中的氨基甲酸酯活性增加,体系内过量的异氰酸酯基团与氨基甲酸酯发生了副反应,体系内NCO含量进一步下降,从而导致产物的黏度进一步增大。
从图4可以看出随着反应温度的升高,平均剥离力呈现出了先增大后减小的变化趋势,并在反应温度为70℃时,平均剥离力达到最大。其原因是反应温度为60℃时,聚醚多元醇与异氰酸酯的反应程度较低,体系中含有较多游离的单体,分子量较小,复合后容易剥离,剥离力较小。反应温度升高到70℃之后,聚醚多元醇与异氰酸酯完全反应,分子量达到最大,剥离力也达到最大。反应温度继续升高,平均剥离力下降可能的原因是体系内过量的异氰酸酯基团发生自聚或是与微量的水分发生副反应,甚至在高温下与氨基甲酸酯发生了副反应,使得体系内氨基甲酸酯含量与NCO含量下降,副产物的含量升高,导致胶黏剂与基膜表面反应时形成的化学键少,降低了胶黏剂的粘结性能,从而使平均剥离力下降。
在实际生产过程中,无溶剂型聚氨酯胶黏剂对黏度具有严格的要求,黏度过高会影响胶黏剂的流动性,导致涂布不均匀、上胶困难等问题,保持较低的黏度可以使胶黏剂更容易施工,从而提高生产效率。所以在反应的过程中需要更加严格的控制温度,才能满足实际生产的需求。对于本实验体系,聚氨酯固化剂最佳的反应温度为70℃。
2.3 R 值对固化剂性能的影响
本实验选择2、2.5、3、2.5、4五种不同的R值,研究R值与合成的聚氨酯固化剂的储存稳定性以及性能之间的关系。合成的聚氨酯固化剂的初始外观均为无色透明,图5和图6所示为不同R值合成的固化剂的黏度以及主剂与固化剂以一定比例配制应用于MOPP复合MOPP的平均剥离力。
由图5可以看出,随着R值的增加,初始黏度不断下降。这是因为TDI的黏度较小,过量的异氰酸酯在固化剂体系中起到降低黏度的作用,使得体系的黏度下降。由表1可以看出,随着R值的增大,聚氨酯固化剂的储存稳定性不断降低,聚氨酯固化剂的R值为2和2.5时,在室温下储存30天后发生了凝胶,可能的原因是体系中过量的异氰酸酯基团与空气中的水分发生反应,在固化剂内生成了聚氨酯脲,同时由于体系的初始黏度较大,聚氨酯分子运动受到限制,导致长时间储存后出现凝胶。而聚氨酯固化剂R值为3、3.5、4时,NCO含量随着R值的增大而增加,使得异氰酸酯基团更容易与水分发生反应,导致体系黏度增大,但其初始黏度较低,所以无表面凝胶的现象。
由图6可以看出,随着固化剂R值的增大,平均剥离力不断减小,原因是聚醚多元醇与异氰酸酯完全反应后,合成的聚氨酯固化剂R值越大,残留的异氰酸酯越多,而相对于聚氨基甲酸酯以及聚醚多元醇,异氰酸酯的分子量非常小,这种稀释效应使得整个体系的平均分子量减小。同时异氰酸酯残留含量越多,越容易在固化过程中与空气中的水分发生副反应,使得聚氨酯胶黏剂与基膜接触时反应固化能力降低,因此粘结性能下降,平均剥离力不断减小。因此综合考虑聚氨酯固化剂的黏度、储存稳定性以及剥离力,选择R值为2.5,可以得到流动性佳,稳定性较好的聚氨酯固化剂。
2.4 异氰酸酯种类对固化剂的影响
由表2可以看出,由MDI和TDI这两种芳香族异氰酸酯合成出的聚氨酯固化剂初始黏度较脂肪族异氰酸酯的IPDI较 大,由MDI合成的聚氨酯固化剂初始黏度远大于TDI,原因是芳香族异氰酸酯具有刚性苯环,苯环的存在会导致分子间作用力变强,从而在反应过程中形成更多的交联结构,增加聚氨酯的分子量,从而导致黏度增加。由于MDI分子量大于TDI,分子量越大,反应过程中分子间相互作用增强,分子之间的聚集更紧密,从而形成更加致密的网络结构,因此MDI合成的聚氨酯固化剂黏度比TDI合成的大。
由图7可以看出,选用不同种类的异氰酸酯对聚氨酯固化剂的粘结性能有着重要的影响,两种芳香族异氰酸酯TDI与MDI都有着较大的平均剥离力,且水煮后性能有所上升,可能的原因是芳香族异氰酸酯相比于脂肪族异氰酸酯具有更紧密的交联结构,经过水煮后,导致固化产物密度更高,聚氨酯分子间的相互作用力更加紧密,同时水分子的渗透可以使得聚氨酯的极性增加,这些因素都会提高聚氨酯的粘结性能。IPDI有着良好的平均剥离力,且在水煮后性能几乎不下降,有着良好的耐水性能,但在粘结性能方面不如TDI与MDI。综合合成的聚氨酯固化剂的黏度、储存稳定性以及性能,可以看出TDI的使用性能最佳。
强于对照组;在精密度测试中,实验组不论是日内精密度还是日间精密度均强于对照组,差异具有统计学意义;提取回收率实验中,实验组的提取回收率明显高于对照组,差异有统计学意义;稳定性实验中,实验组和对照组不同浓度在室温放置12小时,反复冻融3次以及-20℃放置1周的稳定性没有显著性差异;柱压测定方面,在不同流速条件下,实验组的柱压显著低于对照组,差异显著。本研究结果显示乙腈作为流动相用于多西他赛浓度测定在精密度、提取回收率、稳定性以及柱压方面相对于甲醇具有显著优势[23],推荐使用乙腈作为多西他赛浓度测定的常规流动相。
免责声明:部分资料来源于网络,转载的目的在于传递更多信息及分享,仅提供交流平台,不为其版权负责。如涉及侵权,请联系我们及时修改或删除。
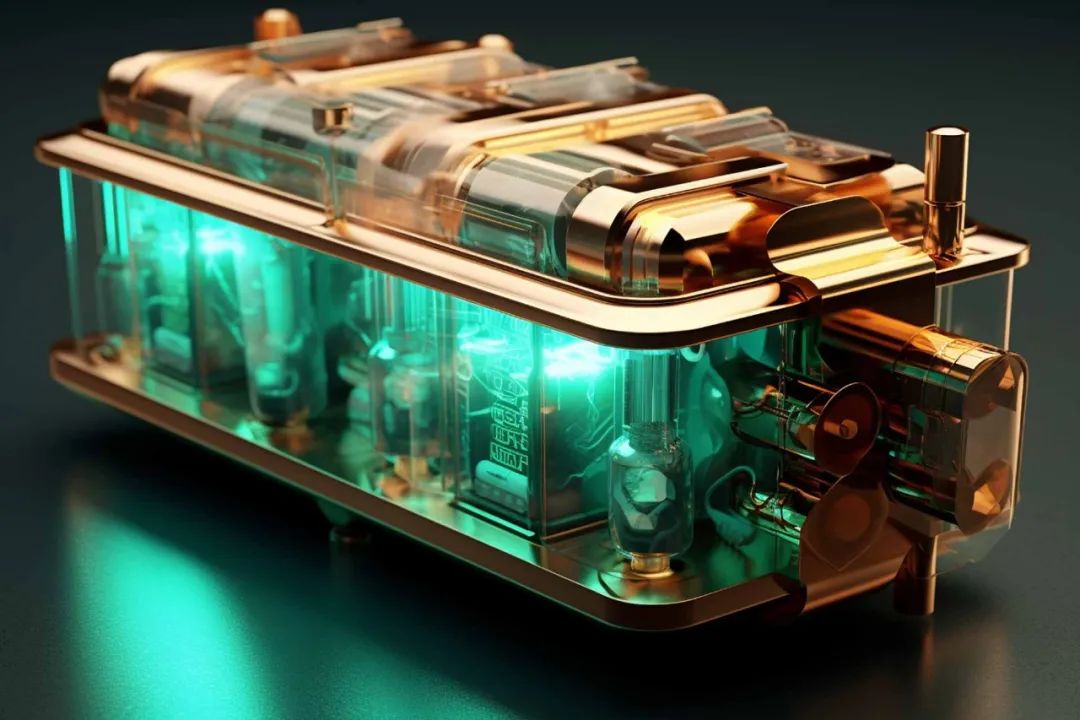
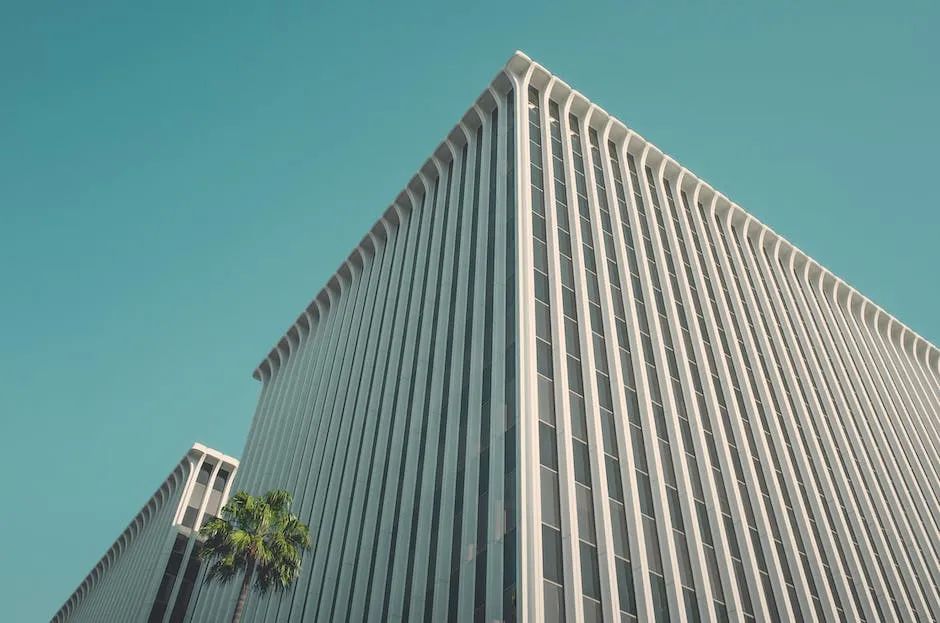